Provide chains are cumbersome to handle and navigate for all companies.
Any inefficiencies, operational turnaround pains, prices related to handbook processes and unpredictable delays will minimize down earnings considerably.
What’s Provide Chain Optimization?
Provide Chain Optimization is the method of enhancing the effectivity and effectiveness of your entire provide chain.
On this weblog, we are going to focus on 5 important optimization practices for provide chain optimization right this moment. These embrace –
- setting clear efficiency metrics (KPIs),
- automating processes,
- negotiating higher phrases with suppliers via SPM,
- enhancing forecasting accuracy,
- optimizing stock administration.
Let’s get began.
Step 1: Setting clear efficiency metrics (KPIs)
Setting clear efficiency metrics, or Key Efficiency Indicators (KPIs), is the cornerstone of any profitable provide chain optimization technique.
KPIs function quantifiable measures that assist companies monitor and assess the effectivity of varied provide chain actions.
With out these metrics, it is difficult to establish areas needing enchancment or to have a good time areas of success.
Begin by understanding your corporation’s major objectives. Are you targeted on decreasing prices, enhancing supply occasions, or enhancing buyer satisfaction? Your KPIs ought to straight replicate these aims.
Imprecise KPIs will not aid you a lot. As a substitute of setting a purpose like “enhance supply occasions,” purpose for “scale back supply occasions by 10% throughout the subsequent six months.” This specificity makes it simpler to measure progress and decide success.
Efficient KPIs ought to cowl all vital elements of your provide chain, from procurement to supply.
Widespread KPIs embrace order accuracy, stock turnover charges, provider efficiency, and buyer satisfaction ranges.
Here’s a complete checklist of metrics you can take into account monitoring, primarily based in your aims. Click on on every goal to discover potential KPIs.
KPI | Calculation |
---|---|
Price Financial savings | (Baseline Price – Precise Price) / Baseline Price x 100 |
Price Avoidance | (Anticipated Price – Precise Price) / Anticipated Price x 100 |
Complete Spend Beneath Administration | Complete Spend Beneath Administration / Complete Procurement Spend x 100 |
KPI | Calculation |
---|---|
Provider On-time Supply (OTD) | (Variety of On-time Deliveries / Complete Deliveries) x 100 |
Provider High quality Fee | (Variety of Acceptable Items / Complete Items Obtained) x 100 |
Provider Compliance Fee | (Variety of Compliant Provider Actions / Complete Provider Actions) x 100 |
KPI | Calculation |
---|---|
Buy Order Cycle Time | Complete Time for All Buy Orders / Variety of Buy Orders |
Procurement ROI | (Financial savings – Price of Procurement Operations) / Price of Procurement Operations |
E-Procurement Utilization Fee | (Worth of E-Procurement Transactions / Complete Procurement Transactions) x 100 |
KPI | Calculation |
---|---|
Contract Utilization Fee | (Worth of Spend Beneath Contracts / Complete Procurement Spend) x 100 |
Share of Spend with Most popular Suppliers | (Spend with Most popular Suppliers / Complete Procurement Spend) x 100 |
KPI | Calculation |
---|---|
Stock Turnover Fee | Price of Items Offered / Common Stock |
Stock Accuracy | (Right Stock Information / Complete Stock Information) x 100 |
Days of Stock on Hand (DOH) | (Common Stock / Price of Items Offered) x 365 |
KPI | Calculation |
---|---|
Sustainable Procurement Fee | (Sustainable Procurement Spend / Complete Procurement Spend) x 100 |
Provider Danger Assessments Accomplished | (Variety of Provider Danger Assessments Accomplished / Complete Variety of Suppliers) x 100 |
Step 2: Automating Processes
Guide processes usually are not solely sluggish and error-prone but additionally expensive.
Automation is a game-changer in provide chain administration.
By leveraging expertise, companies can automate repetitive and time-consuming duties and liberate beneficial human assets for extra strategic duties.
This results in sooner turnaround occasions, improved accuracy, and a extra environment friendly provide chain.
Key Parts and Applied sciences Concerned
Beneath are the important thing elements of a contemporary automated provide chain workflow.
Optical Character Recognition & Clever Doc Processing
By automating information entry and extraction, OCR reduces human error and hurries up info processing. That is significantly necessary when dealing with complicated provide chain paperwork like invoices, buy orders, and delivery manifests.
Workflow Automation and Integrations
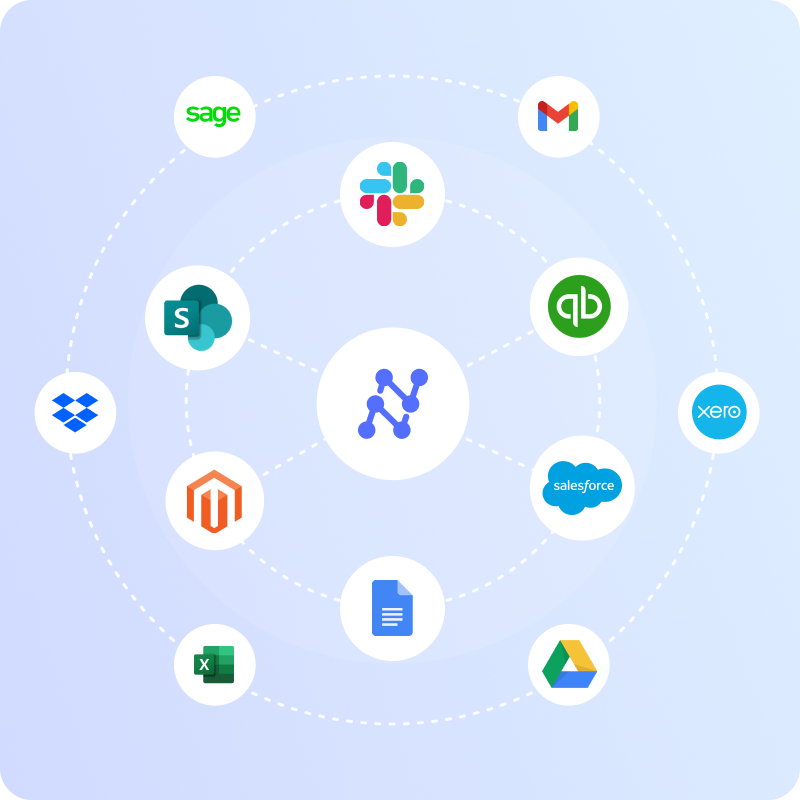
Workflow automation streamlines the circulation of duties and data between totally different apps and databases. This ensures clean operations and real-time visibility all through the availability chain.
Accounts Payable (AP) Automation and Bill Matching
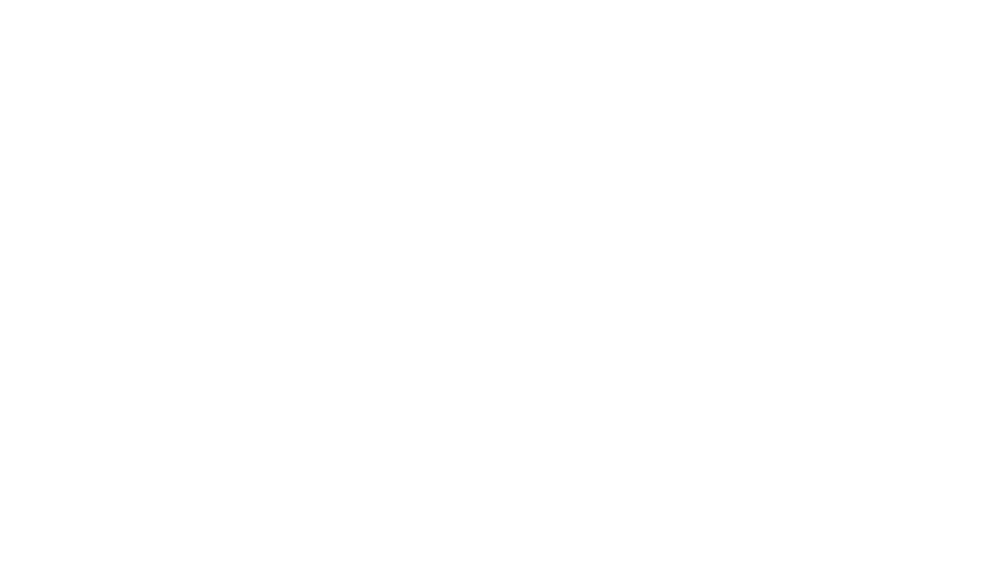
AP automation simplifies your entire accounts payable course of, from receiving invoices to creating funds.
Firstly, this expertise automates bill seize, approval workflows, and fee processing, considerably reducing down processing occasions and errors.
Secondly, bill matching is a crucial a part of AP automation, making certain correct matching of invoices with buy orders and receiving paperwork, stopping discrepancies and fraud.
Thirdly, integrating AP automation with accounting software program ensures seamless information circulation, enhancing accuracy and effectivity in monetary administration. This integration eliminates handbook information entry, reduces the chance of errors, and supplies real-time visibility into monetary transactions, enabling higher decision-making and monetary management.
Robotic Course of Automation (RPA)
.png)
RPA entails utilizing software program robots to automate repetitive duties. In provide chain administration, RPA can streamline actions similar to order processing, stock monitoring, information entry, and customer support operations.
To get began with provide chain automation, learn our in-depth weblog on how you can automate your provide chain by clicking under –
The Ultimate Guide to Supply Chain Automation
The ultimate guide to supply chain automation. Discover key technologies, top software of 2024, and practical implementation insights.
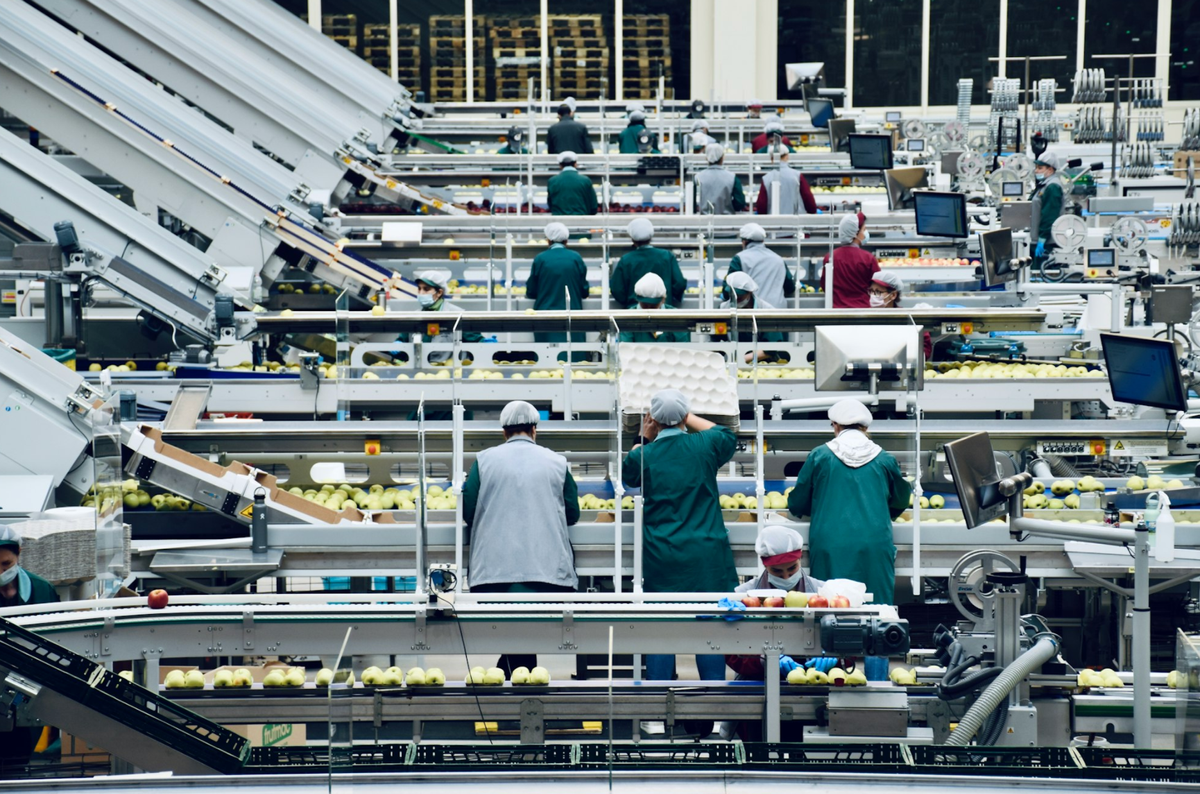
Step 3: Negotiating higher phrases with suppliers via SPM
Suppliers’ efficiency administration, or SPM, is the strategic method of managing and optimizing suppliers’ efficiency.
This entails appraisal and administration of the operations of a provider to make sure that most worth is obtainable to the corporate.
Good SPM permits an organization to:
- Improve efficiency and enhance reliability of suppliers
- Scale back provider danger and the impression from provide chain disruptions
- Get higher costs
- Enhance high quality and requirements of compliance
Easy methods to Implement SPM?
Think about the next steps to get began with SPM in your provide chain.
Step 1: Phase Suppliers and Use Filters
There are a selection of suppliers with various significance to your organization. The suppliers which are vital, these which are necessary and those that don’t make a big impression.
Learn extra on identification of key suppliers under.
Key Suppliers | Identify & Manage Key Vendors & Suppliers
Identifying, monitoring, and managing key suppliers can help your business reduce risk, save money, and foster innovation.
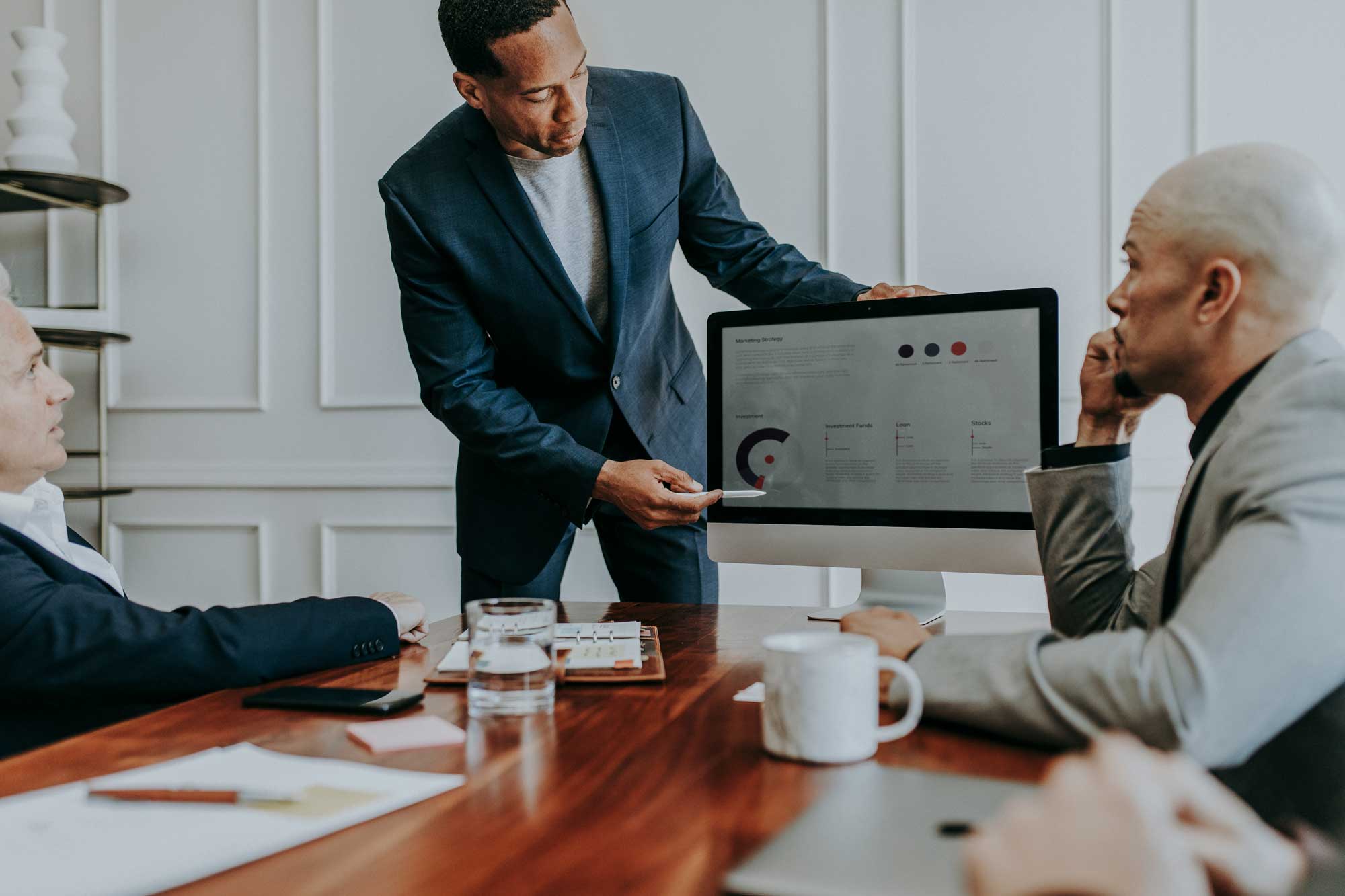
Step 2: Outline Efficiency Measures
Develop express, measurable efficiency measures of suppliers. Widespread metrics embrace supply efficiency, high quality requirements, compliance with laws, and cost-effectiveness. Learn extra under.
What are supplier performance measures? | ADR International
ADR International
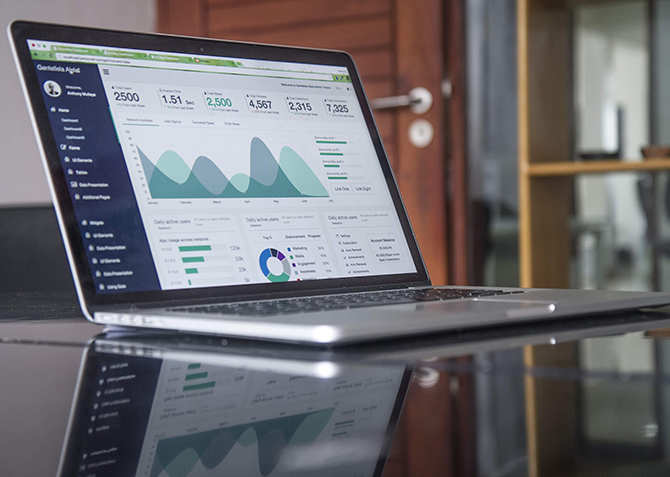
Step 3: Keep a Provider Scorecard
Create a provider scorecard to trace and consider provider efficiency in opposition to the outlined metrics. This ought to be a dynamic doc that’s usually up to date with efficiency information.
Step 4: Conduct Common Efficiency Opinions
Conduct common efficiency opinions along with your vital suppliers. Feed into that the information from the scorecard to debate their efficiency, focus on any issues, and be taught what alternatives there are for enchancment.
Step 5: Negotiate Higher Phrases
Leverage the information and insights derived throughout SPM to barter higher / improved phrases along with your suppliers. You possibly can level out the place precisely they lack and provide mutually useful adjustments in contracts.
7 Tips for Negotiating Better Payment Terms With Your Suppliers
One of the most effective ways to improve your cash flow is to lengthen your payment terms with vendors and suppliers. Learn how to do it.
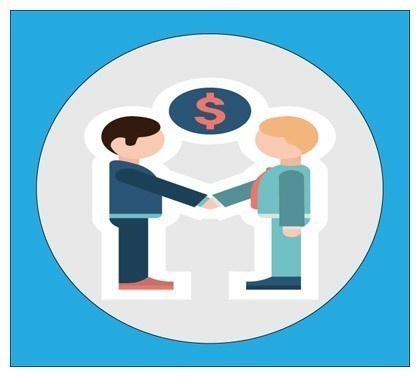
Step 4: Enhancing forecasting accuracy
Correct forecasting is vital to provide chain optimization.
By predicting future demand, companies can guarantee they’ve the precise merchandise in the precise portions on the proper time, decreasing extra stock and minimizing stockouts. Provide chain forecasting could be quantitative or qualitative.
Quantitative forecasting depends on numerical information and statistical strategies to foretell future developments. These strategies are greatest when you’ve ample historic information and a comparatively secure setting –
- Exponential Smoothing: Makes use of weighted averages of previous information, giving extra significance to latest observations. Splendid for short-term forecasts and straightforward to implement with the precise instruments. Instance: Predicting subsequent month’s gross sales primarily based on latest gross sales developments.
- Adaptive Smoothing: A sophisticated model of exponential smoothing that adjusts weights primarily based on information fluctuations. Requires automation instruments for real-time information processing. Instance: Adapting gross sales forecasts shortly in response to sudden market adjustments.
- Shifting Common
- Regression Evaluation
- Life Cycle Modeling
For a deeper dive into these strategies, do an online search to discover extra detailed assets and case research. This introduction goals to offer you a place to begin to boost your provide chain forecasting successfully.
Qualitative forecasting makes use of knowledgeable opinions, market analysis, and different non-quantifiable info. It is helpful when historic information is restricted or not relevant.
- Market Analysis: For instance, conducting buyer surveys to foretell demand for a brand new product.
- Delphi Methodology: Course of entails gathering insights from a panel of consultants via a number of rounds of questioning. This reduces bias and reaches a consensus on future developments. Instance: Forecasting long-term trade developments by consulting with market analysts.
Step 5: Optimizing stock administration
Stock optimization is all about managing inventory ranges strategically throughout an organization’s provide chain to chop prices, make prospects happier, and increase earnings.
Should you do not handle your stock properly, you’ll run into huge issues like shedding income since you’re out of inventory and losing cash on extra stock that simply sits on the cabinets.
Now, let’s dive into one of many strategies that companies use to optimize their stock.
ABC Evaluation is a listing categorization methodology that divides gadgets into three classes (A, B, and C) primarily based on their significance to the enterprise.
Class A gadgets are essentially the most beneficial, Class B gadgets are of average worth, and Class C gadgets are the least beneficial. This methodology helps companies prioritize their stock administration efforts to give attention to essentially the most vital gadgets.
Think about a small retailer specializing in digital items similar to smartphones, laptops, equipment, and residential home equipment. This retailer goals to implement stock management utilizing the ABC system to categorise merchandise primarily based on their significance and worth to the enterprise.
These are the steps the retailer would comply with –
1. Collect Knowledge: Acquire gross sales historical past for the final yr. Acquire the acquisition costs of every merchandise. Observe the utilization fee/frequency of every merchandise.
2. Assign a Worth to Every Merchandise: Calculate the greenback worth every product has generated within the final yr. Assign weights primarily based on income, with the best dollar-value gadgets receiving the best weights.
3. Categorize Objects: As soon as carried out, the categorization would possibly appear to be this –
- Class A: Merchandise producing 70% of the entire income; for instance, smartphones and laptops.
- Class B: Merchandise producing 20% of the entire income; for instance, high-end equipment.
- Class C: Merchandise producing 10% of the entire income; for instance, miscellaneous equipment and small dwelling home equipment.
4. Alter Stock Ranges: Stock ranges can now be adjusted for every merchandise primarily based on it is categorization.
- Class A: Keep the next stock to keep away from stockouts.
- Class B: Keep a medium stage of stock, balancing availability and carrying prices.
- Class C: Hold restricted inventory and order as wanted.
By following this strategy, the retailer can successfully prioritize stock administration efforts, making certain that essentially the most vital gadgets are all the time obtainable whereas minimizing carrying prices for much less important gadgets.
Another strategies embrace –
- Financial Order Amount (EOQ)
- Simply-In-Time (JIT) Stock
- Security Inventory Stock
- Reorder Level Components
- Consignment Stock
For a deeper dive into these strategies, do an online search to discover extra detailed assets and case research. This introduction goals to offer you a place to begin to boost your provide chain forecasting successfully.
Conclusion
Provide chain optimization is not only a one-time factor, however moderately an ongoing journey that requires steady effort and a focus.
By implementing the 5 important practices we mentioned on this weblog, you’ll be able to considerably enhance the effectivity and effectiveness of your provide chain.
And this is the factor: there are much more strategies you’ll be able to discover by yourself. Companies must consistently monitor and modify their methods to adapt to altering market circumstances and technological developments.
By staying proactive and dedicated to steady enchancment, you’ll be able to flip your provide chain right into a aggressive benefit for your corporation.